
December 23, 2024
How Robots Are Saving Companies Millions in Equipment Downtime
In today’s competitive industrial landscape where optimization and innovation go hand in hand, both predictive maintenance and robotics have proven to provide clear financial advantages to companies.
For instance, industries such as automotive production, heavy manufacturing, and oil and gas can suffer up to $22,000 per minute of maintenance spending. Considering these costs, even the slightest enhancement in operational efficiency can result to worthwhile savings - something that predictive maintenance strategies have proven to achieve by allowing companies to detect equipment issues and prevent them from escalating.
According to a recent survey of manufacturers in the United States, those who used predictive maintenance can enjoy up to 18.5% reduction in unplanned downtime costs and a remarkable 87.3% decrease in defects compared to teams using traditional preventative maintenance methods.
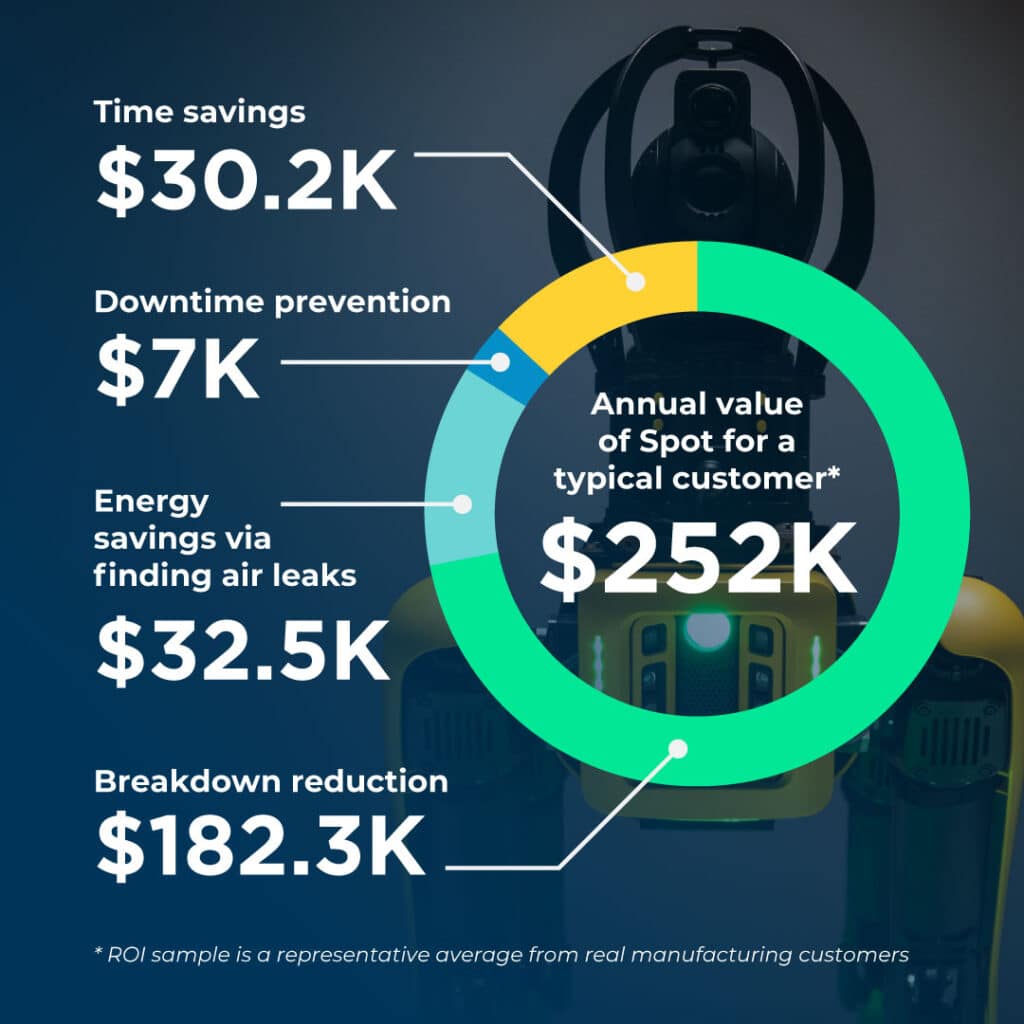
Many organizations today have begun adopting condition monitoring programs to identify early signs of equipment damage and failure to lessen repair costs and maximize their lifecycle. Key metrics these programs monitor include acoustic anomalies, atypical vibrations, electrical faults, energy consumption variations, low lubricant levels, and temperature fluctuations. Specialists can track these indicators over time to detect anomalies and trends, paving the way for more proactive repairs that enhance operational efficiency and extend the lifetime of the equipment.
Organizations are increasingly adopting condition monitoring programs to identify early signs of equipment failure. Key metrics monitored include temperature fluctuations, acoustic anomalies, atypical vibrations, pressure changes, energy consumption variations, electrical faults, and low lubricant levels. By tracking these indicators over time, reliability teams can spot performance trends and anomalies, enabling proactive repairs that extend equipment life and enhance operational efficiency.
While predictive maintenance can provide immediate benefits, companies must also consider its implementation costs across their processes. Companies typically choose from three primary data-capture methods:
- Manual Inspections: Technicians use specialized tools to conduct them by hand.
- IoT-Enabled Fixed Sensors: These monitor critical assets and have gained popularity with the rise of Industry 4.0.
- Robotics: Recent advancements have made robots essential for automating inspection processes.
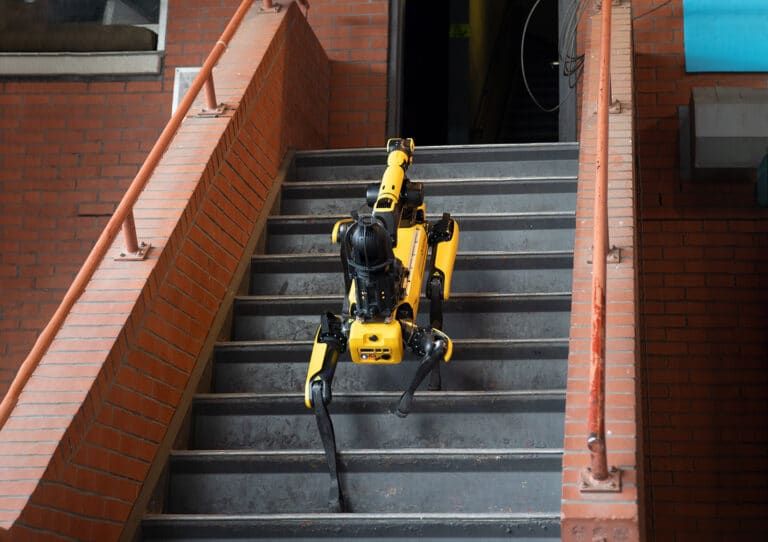
Each method incurs costs related to sensor hardware, connectivity infrastructure, software for data analysis and alerts, cybersecurity measures, and labor for deployment and maintenance. Mobile industrial robots like Boston Dynamics' Spot have emerged as a cost-effective solution for scaling predictive maintenance efforts. Unlike fixed sensors that require extensive infrastructure, mobile robots can traverse facilities to monitor multiple assets efficiently. This flexibility reduces the need for numerous fixed units while streamlining operations.
Automation enhances these advantages further. Robots like Spot can conduct hundreds of inspections in a single mission, generating thousands of data points daily across various locations. This comprehensive data collection supports effective predictive maintenance while allowing human workers to focus on more complex tasks.
As industries increasingly adopt robotics, the financial benefits of predictive maintenance and automated inspections become more apparent. For companies aiming to minimize downtime and improve efficiency, investing in robotics not only provides a technological edge but also promises significant financial returns.